Digital transformation is reshaping all areas of manufacturing, and the automotive industry is no exception. The implementation of the Internet of Things (IoT) in automotive production plants enables real-time monitoring of machinery and processes through the use of advanced sensors and digital platforms. This technology not only improves operational efficiency but also enables predictive maintenance and data-driven decision-making.
In this article, we’ll break down how an IoT system works in the automotive industry and highlight the key benefits it brings.
How Does IoT Work in the Automotive Industry?
1. IoT Sensor Implementation 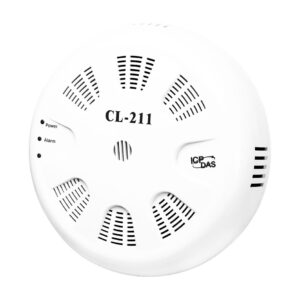
It all starts with installing smart sensors like the CL-211, which are placed on critical machinery to monitor key variables such as temperature and humidity. These devices collect real-time data about equipment conditions and production performance.
2. Data Acquisition and Transmission
The data captured by the sensors is transmitted to a central controller via Modbus RS485 communication modules like the AI-AN-2000. This step ensures a constant connection between the sensors and the industrial network.
3. Real-Time Data Management
The collected data is wirelessly transmitted to the AI-AG-3003 gateway, where it is stored and then uploaded to the cloud via Ethernet. Using the AI-AP-1YP annual license, the data is analyzed and managed through a dedicated IoT platform. This license enables real-time visualization of OEE (Overall Equipment Effectiveness) for machines, production lines, and the entire plant.
4. Dashboard Monitoring
All data is displayed on interactive dashboards that are accessible from any web browser—whether on a phone, tablet, HMI, PC monitor, or an industrial Panel PC like the PPC-Z153PW-B61A1. These dashboards display charts, tables, and alerts, helping operators quickly identify process deviations before they escalate.
5. Automated Responses 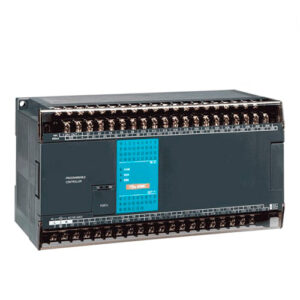
When abnormal conditions are detected, the IoT system can trigger automatic responses—such as adjusting operating parameters or initiating preventive shutdowns—using controllers like the FBs-60MCR2-AC PLC.
6. Alerts and Notifications
In the event of failures or imminent risks, the system—powered by cloud-based platforms like Auk Industries—can send real-time alerts to technicians via email or WhatsApp, ensuring a rapid response and minimizing downtime.
Benefits of IoT in Automotive Production
-
Operational Efficiency: Detects issues early to reduce downtime.
-
Predictive Maintenance: Optimizes maintenance schedules and prevents unnecessary interventions.
-
Transparency: Provides full visibility into equipment and process status.
-
Cost Reduction: Reduces repair and unplanned downtime costs.
-
Sustainability: Ensures optimal resource usage through efficient operations.
Conclusion
IoT is transforming the automotive industry by integrating advanced technologies that monitor, analyze, and optimize production processes. The result is higher performance, smarter decision-making, and better control over operations.
At Logicbus, we offer a full range of industrial IoT solutions designed to make your automotive plant smarter, more connected, and more efficient.
Ready to modernize your production line?
Contact us today and discover how our IoT solutions can drive your operations forward.
sales@logicbus.com | support@logicbus.com | +1 619 616 7350 | Start conversation