The ATD must be kept at a consistent temperature before testing. An ATD must be soaked and held at 69-72 degrees Fahrenheit for four hours before testing. This is required by the FMVSS208 standard. It is required to record the length of the soak and the minimum and maximum temperature and humidity during that time.
The temperature of the ATD affects the accuracy of the testing. The temperature range during the soak is extremely specific and needs to be held to because the elastomeric material in the abdomen and rib cage of the ATD can behave differently under temperature extremes. Vast differences in temperatures before the test could lead to inconsistent crash test results and unreliable performance. Ultimately, unregulated temperatures before the test can cause false passes or failures.
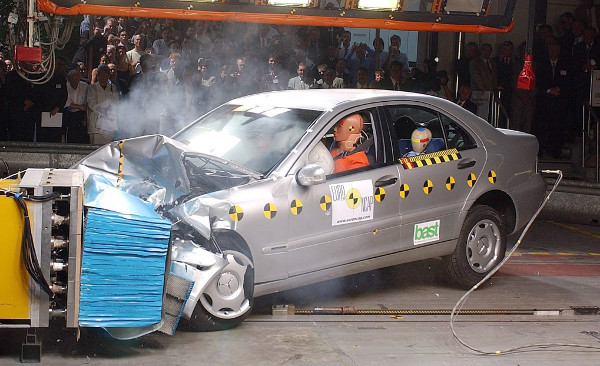
Temperature extremes can cause test delays. If the ATD’s temperature is found out of range before the test is about to begin, it could delay a test for a minimum of four hours. The ATD would need to be re-soaked, essentially re-starting the process. This results in the customers—OEMs or tier suppliers—being delayed. Further implications would be lost test facility usage time and customer delays in product validation.
Sensors are used to monitor temperatures. Throughout the process, sensors are used to monitor the temperature of the ATD. This begins during the soaking and continues through the crash test, to ensure the ATD has remained at a consistent temperature. Sensors provide the pinpoint accuracy needed to closely monitor the temperature needed throughout the process.
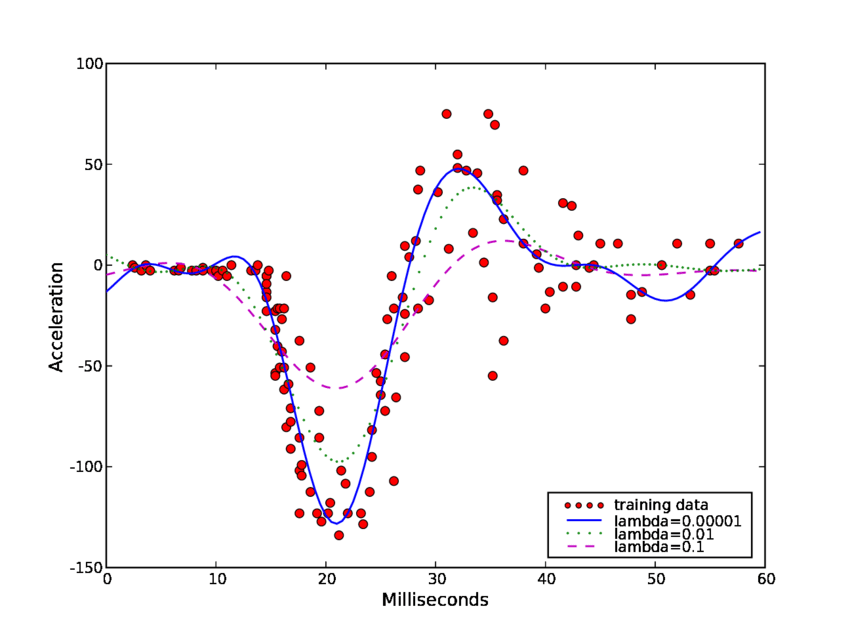
Currently, data isn’t often monitored live. Sensor data is downloaded after a crash test. A test facility can be caught off-guard that an ATD is out-of-spec when it was expected to be functioning properly. Using wireless monitoring would allow testers to know immediately if something isn’t right during the test. Currently, if an ATD is out-of-spec it will delay the process by a minimum of four hours.
Using wireless sensors allows test operators to measure the ATD’s temperature to know whether it’s out-of-spec at any point during the testing process. Testing customers that have switched to wireless sensors say this increase in efficiency helps reduce the time lost due to unregulated ADT’s, and ensures results are accurate and consistent.
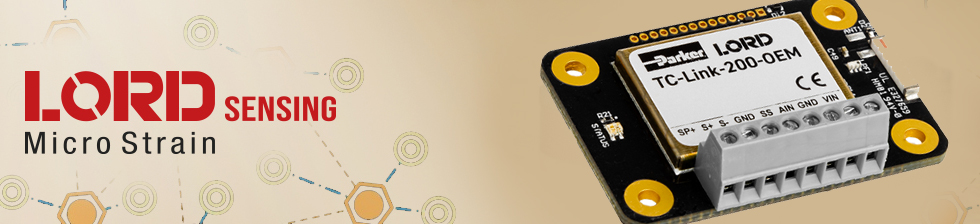
Learn more about MicroStrain wireless sensing solutions.
Visit our website:
www.logicbus.com
sales@logicbus.com | support@logicbus.com | +1 619 616 7350 | Start conversation