In industrial automation, weighing is the calculation of the mass of a given product, raw material, component or vehicle.
When speaking of weighing systems, reference is often made to load cells, i.e., electronic transducers that measure the force applied on an object by means of an electrical signal that varies as the deformation that the force in question produces on the transducer changes. So it is in electronic weighing systems and in the measurement of mechanical compressive and tensile forces in the logistics, transportation, building construction, laboratory, robotics, scale manufacturers, and food industries that load cells find their main applications.
Load cells are transducers that convert compressive, tensile, torsional, pressure, or rotational forces into an electrical signal.
They are used for measuring force and weight (from micrograms to tons). They usually generate an analog signal as an output that is amplified through special acquisition boards.
- Design features: single point, tension/compression, cantilevered
- Applications: industrial electronic weighing systems, mechanical strain measurements, weighing of trucks, rail cars, ships, cranes, hoppers and tanks, batching of food products.
- Models: analog, digital, miniature, specialty for automotive, robotics, metrology, hazardous areas.
Principles of load cell measurement.
LVDT (Linear Variable Differential Transformer)
Load cell based on inductive displacement transducers. The force applied to the platform compresses the spring and moves the moving crew of the LVDT. The latter provides an output proportional to the displacement and thus to the force. They are suitable for precision measurements.
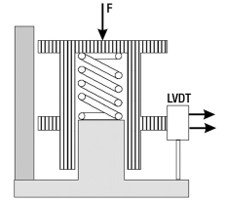
The load cell includes four strain gauges placed along the ring of the cell. The applied force causes an elongation of strain gauges R2 and R4 and a compression of strain gauges R1 and R3. This bridge configuration is such that it gives the maximum voltage change as a result of load application, while the unbalance due to temperature change is minimal. Can be used in stationary measurements.
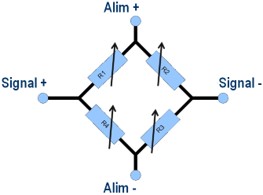
Applying a force to the surface of a piezoelectric crystal generates a charge buildup proportional to the force. The surfaces of the piezoelectric material behave like the faces of a capacitor. Piezoelectric load cells possess a high response rate, however, because of the leakage current the voltage supplied by the charge amplifier tends to decrease. This makes them suitable for vibration measurements.
I/O modules for load cells
SENECA I/O modules for strain gauge load cells can be integrated into all weighing systems in a flexible form. In addition to weight, force or strain gauges, the ‘SG’ modules allow data acquisition in stand-alone mode or interfaced with third-party systems. The devices provide multiple methods of calibration of the load cell connected directly by web server (TCP-IP, Profinet models) with or without dedicated software, with or without weight cam-pion, with or without acquisition of factory parameters The modules are available with Z (17.5×102.5×111 mm) and R (53.3x 90×32.2 mm) form factors depending on installation requirements.
Measurement, made in 4- or 6-wire technique, is available via ModBUS RTU, ModBUS TCP-IP, CANopen, Profinet IO communication protocols and mA V analog output (where available). SG modules directly power the strain gauge and provide primary characteristics of robustness, safety and accuracy with galvanic isolation up to 1,500 Vac. The accuracy class is 0.01 with load cell sensitivity from 1 to 64 mV /V.
The newer modules benefit from very high accuracy due to the presence of a predictive algorithm based on Kalman filter, which was also used to solve the trajectory estimation problem within the Apollo space program.
Hot swapping allows its replacement without interrupting the continuity of the weighing system. Advanced features include versatile application management (counting, automatic tare reset, alarm threshold, automatically upgradable firmware) and measurement (integer or floating point value, stabilization via predictive algorithm and noise filter, configurable resolution and sampling rate). ModBUS models also support the Pass-Through function that allows them to divert requests from Modbus TCP-IP nodes to the RS 485 serial line and behave as gateways.
SENECA’s solution for weighing systems includes an equalization and connection system for up to 4 load cells in parallel SG-EQ4, as well as the availability of OLED (S401) LED (VISUAL ) and IIoT (SSD) HMIs, controllers, radio modules, and gateways for remote signal transmission.
sales@logicbus.com | support@logicbus.com | +1 619 616 7350 | Start conversation